Vermeidung bzw. Eliminierung von Frühausfällen durch künstliche Alterung/Qualifikation
Angewandte Normen
- AEC-Q100
- AEC-Q200
- ANSI/ESD
- DIN
- ECSS-Q-ST-60
- EEE-INST-002
- J-STD-002
- J-STD-020
- JESD
- JIS-C-5321
- JS-001
- MIL-STD-202
- AS6081
Mögliche Anwendungsbereiche:
- Vermeidung von Frühausfällen durch Voralterung/beschleunigte Alterungstests
- Qualifikationen
- Klimabeständigkeit
- Lebensdauerprüfung
- Überlastungstest
- Parameterprüfungen
- ESD-Test (Überprüfung der Empfindlichkeit gegenüber elektrostatischen Entladungen)
- Dichtigkeitsprüfung (Helium-Leck Test)
- Bond-Pull-Test/Bond-Shear-Test
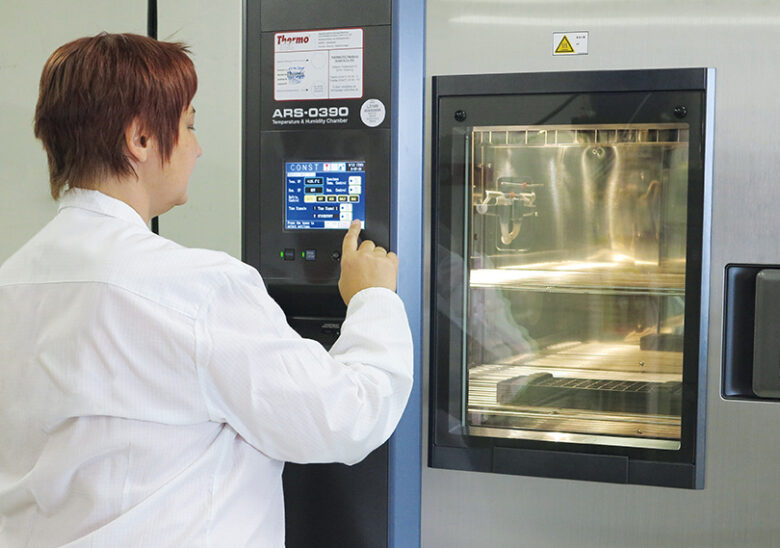
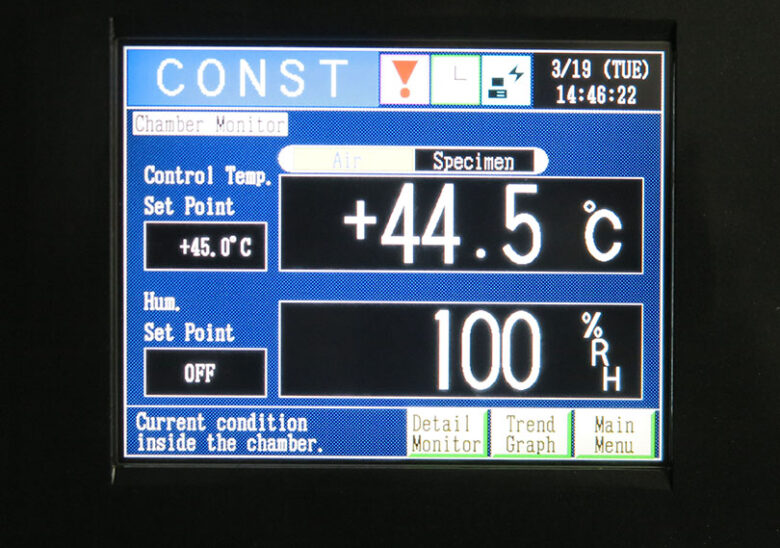
Zur Erhöhung der Qualität und Zuverlässigkeit eines Produkts stellt das Eliminieren von Frühausfällen durch Voralterung in der Serienfertigung nach verschiedenen Normen und Standards eine essentielle Testdienstleistung dar. Mithilfe einer Vielzahl möglicher Methoden (u. a. Burn- In, Hochtemperaturlagerung) nimmt die künstliche Alterung Betriebszeit im Zeitraffer vorweg.
Bei der Hochtemperaturlagerung (HTL) z. B. werden die Bauteile in einem Hochtemperaturschrank bei Temperaturen von beispielsweise 100°C bis 150°C (abhängig vom Bauteil) gelagert. Die Dauer der Lagerung ergibt sich hierbei aus dem gewünschten Zeitraffungsfaktor. Beim statischen Burn-In werden die Bauteile im Burn-In Schrank mit angelegter Versorgungsspannung für beispielsweise 168 Stunden bei 125°C gealtert, was einer ungefähren Betriebszeit von einem halben Jahr entspricht. Da die Ausfallrate von vielen Komponenten dem typischen Verlauf der Badewannenkurve folgt, können so, nach anschließender Prüfung und Bewertung der Bauteile, die meist durch Qualitätsschwankungen verursachten Frühausfälle eindeutig identifiziert und aussortiert werden.
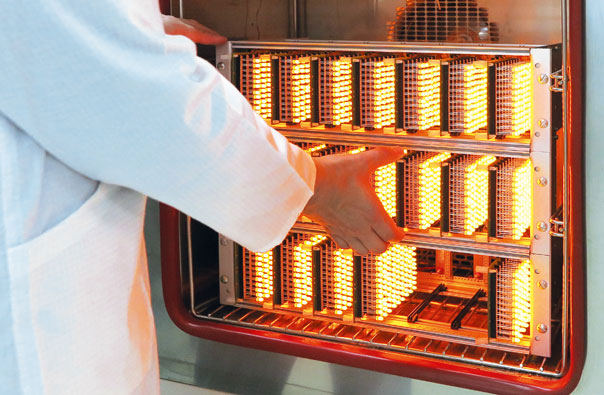
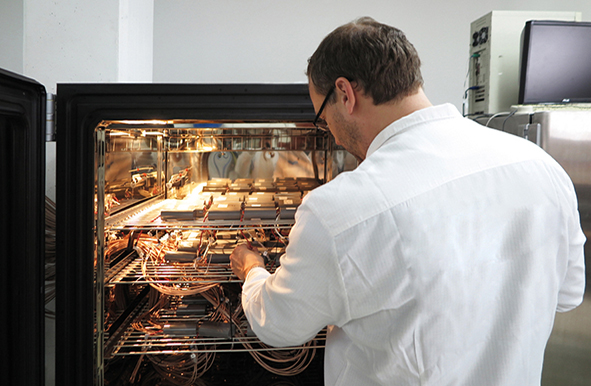
Ob Bauteile ihren Datenblattwerten oder bestimmten kundenspezifischen Vorgaben genügen, wird mithilfe der Qualifikation, der speziell bei sicherheitsrelevanten oder Automotive-Anwendungen vor dem endgültigen Serieneinsatz große Bedeutung zukommt, festgestellt. Bei einer Qualifikation werden nach einer protokollierten Parametermessung an Neuteilen gleichartige Bauteile verschiedenen Prozeduren zur Voralterung oder Nachahmung der Bedingungen des späteren Einsatzgebietes (z. B. Klimatest) unterzogen. Während dieser Behandlung erfolgen Zwischenmessungen und nach Abschluss eine Schlussmessung. Treten bei den darauffolgenden Tests durch die veränderten Umgebungsbedingungen (z. B. hohe Temperatur und Luftfeuchte, elektrostatische Aufladung) Messabweichungen zur Parametermessung auf, so müssen diese individuell interpretiert und ausgewertet werden.
Methoden zur Überprüfung der Klimabeständigkeit:
- statischer Burn-In (gleichbleibende Parameter)
- dynamischer Burn-In (Variation verschiedener Parameter)
- Temperaturlagerung (von -60°C bis +250°C)
- dynamische Hochtemperaturlagerung/Temperatur-Wechsel-Belastung
- Temperaturschock
- Tests bei geregelter Temperatur und Luftfeuchte (konstant oder zyklisch)
- Pressure-Cooker, z. B. HAST (Highly Accelerated Stress Test)
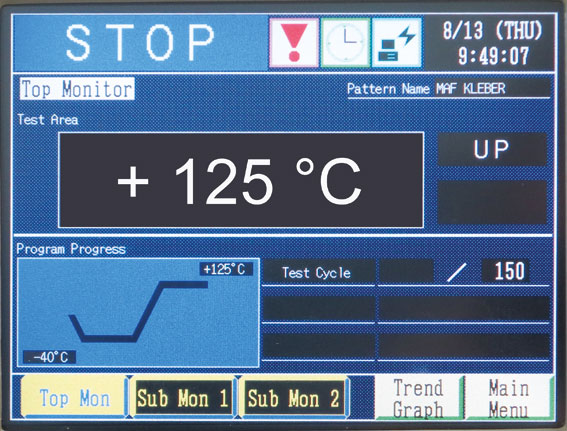
Tests mit Temperaturschock von -60 bis +125 °C sind insbesondere für die Branchen Luft und Raumfahrt sowie Militär von essentieller Bedeutung
Prüfungen wie z. B. Überlastungstests und Lebensdauerprüfungen können die Qualifikation sinnvoll ergänzen. So können Bauteile (z. B. Temperaturfühler, Dünnschichtemitter, Dioden, Stabkerndrossel, …) durch viele verschiedene Lebensdauerprüfungen beispielsweise gemäß AEC-Q100 und AEC-Q200 für den Einsatz im Automobilbereich qualifiziert werden. Auch weiterführende analytische Untersuchungen, z. B. hinsichtlich Veränderungen der Bauteilanschlüsse durch Temperaturbeaufschlagung, sind mithilfe einer Vielzahl von Analysemethoden (z. B. Röntgen, Erstellung von Schliffbildern, mikroskopische Untersuchungen) möglich.