Prevention and elimination of premature failures via artificial aging and qualification
Applied standards
- AEC-Q100
- AEC-Q200
- ANSI/ESD
- DIN
- ECSS-Q-ST-60
- EEE-INST-002
- J-STD-002
- J-STD-020
- JESD
- JIS-C-5321
- JS-001
- MIL-STD-202
- AS6081
Possible applications:
- Prevention of premature failures via pre-aging, i.e., accelerated aging tests
- Qualifications
- Climatic resistance
- Service life-cycle evaluation
- Endurance testing
- Parameter testing
- ESD testing (Evaluation of component’s vulnerability to electrostatic discharge)
- Leak testing (helium leakage test)
- Bond pull testing/bond shear testing
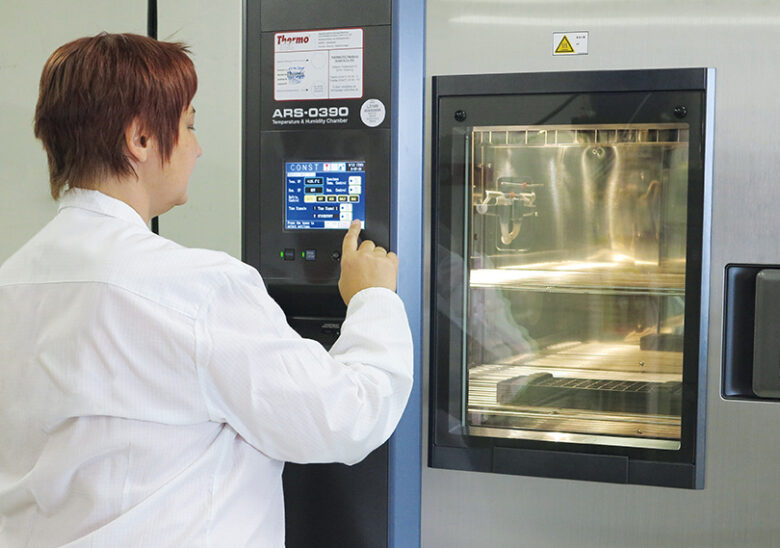
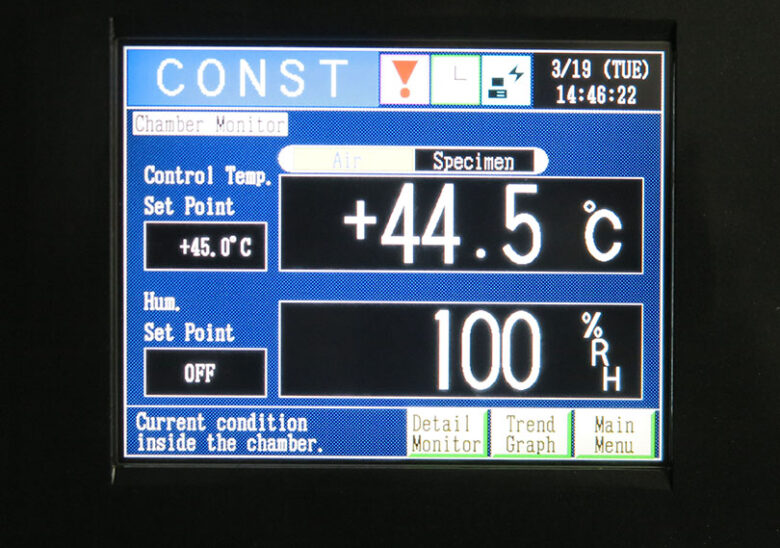
Eliminating premature failures via pre-aging during serial manufacture in accordance with various norms and standards is an essential evaluation service regarding raising a product’s quality and reliability. You can practically fast-forward through a component’s runtime via artificial aging, using a multitude of possible methods, e.g., burn-in or high temperature storage.
At High temperature storage (HTS) the components are stored in a high temperature cabinet at temperatures from 100°C up to 150°C (depending on the individual component). The storage time is derived from the required time lapse factor. With Static Burn-In the components are aged in a burn-in cabinet using applied supply voltage at, for example, 125° C for a time span of 168 hours, which is equal to an approximate runtime of half a year. As the failure rate of many components follows the typical bathtub curve, it is possible to definitively identify and sort out those components of varying quality, which are usually the cause of premature failures.
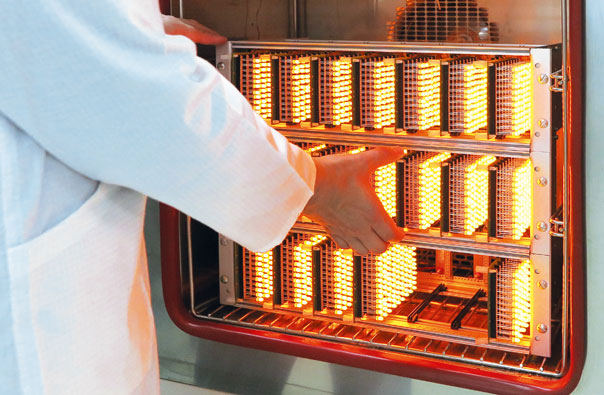
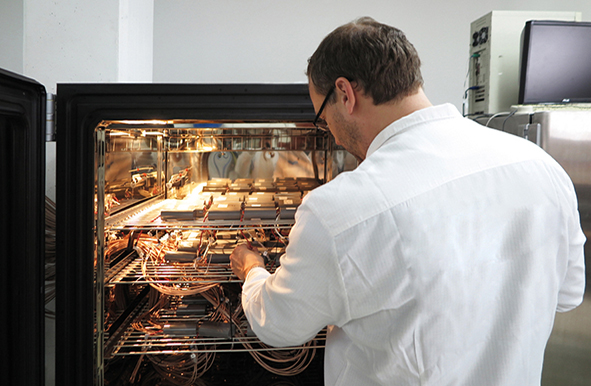
Whether components can satisfy their datasheet requirements or certain customized stipulations is determined before the final serial use through qualification, which is especially important in safety-relevant or automotive applications. Following a recorded measuring of parameters from newly manufactured components, qualification has similar components put through various procedures to either pre-age them or to simulate the conditions of their future area of application, e.g. climatic resistance. Intermediate measurements are taken during this process, followed by a final measurement. Should the changed environmental conditions (for example, high temperature and humidity, electrostatic charge) cause deviations from the measured parameters during the subsequent tests, it becomes necessary to interpret and evaluate those deviations individually.
Methods to evaluate climatic resistance:
- Static burn-in (constant parameters)
- Dynamic burn-in (variation of different parameters)
- Storage at different temperatures (from -60°C to +250°C)
- Dynamic high temperature storage/temperature-change stress
- Thermal shock
- Testing at controlled temperatures and humidity (constant or cyclic)
- Pressure cooker, i.e., HAST (Highly Accelerated Stress Test)
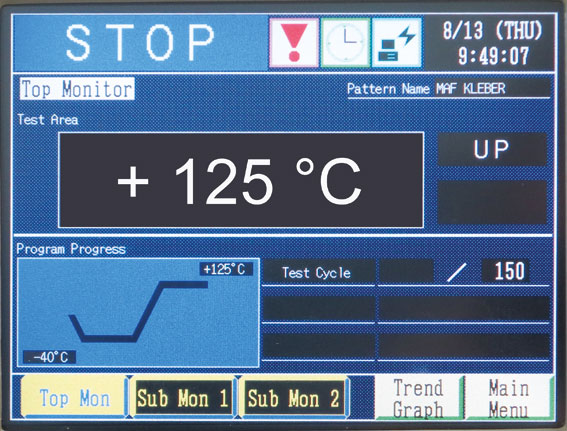
Temperature shock testing, ranging from -60 up to +125 °C is essentially important for both commercial and military aerospace industries
Tests like endurance testing and life-cycle evalution are useful additions to the qualification process. This allows for example to qualify components (e.g. temperature sensors, thin-film emitters, diodes, rod core chokes, …) via various life-cycle evaluations in accordance with AEC-Q100 and AEC-Q200 to be used in the automotive sector. Further analyses, for example concerning changes of the component connections through temperature exposure are possible, using a multitude of analytical methods (e.g., x-rays, cross-sectioning, microscopic analysis).