Applied standards
- IEC 62402
- VDMA 24903
HTV services in regards to obsolescence management
Lectures/workshops at the HTV academy
Long-term storage of components
Qualifying electronic components
Uncovering component counterfeiting
Refurbishing electronic components and assemblies
Obsolescence management, an overview:
- Reactive obsolescence management
- Responsibilities of obsolescence managers
- Obsolescence management guideline and obsolescence management plan (OMP)
- Risk analysis for complex units
- Corrective measures in cases of obsolescence
Obsolescence management
Electronic components are frequently subjected to product change notifications (PCN) and product discontinuation notices (PDN), which affects every industrial branch, all over the world. Costly supply bottlenecks are the result when much needed components, materials or tools are no longer available from their original manufacturer in their original specification. This is known as obsolescence.
A proactive obsolescence management is thus more than vital for companies to reduce or fully avoid unbudgeted costs. Obsolescence can hit every branch of the capital goods industry (investment goods, infrastructure, long-term consumables and software products) since electronic components only have a production life cycle of a few years at best. Some products may even come out with components that are already obsolete if the developers haven’t made any appropriate specifications during the development phase.
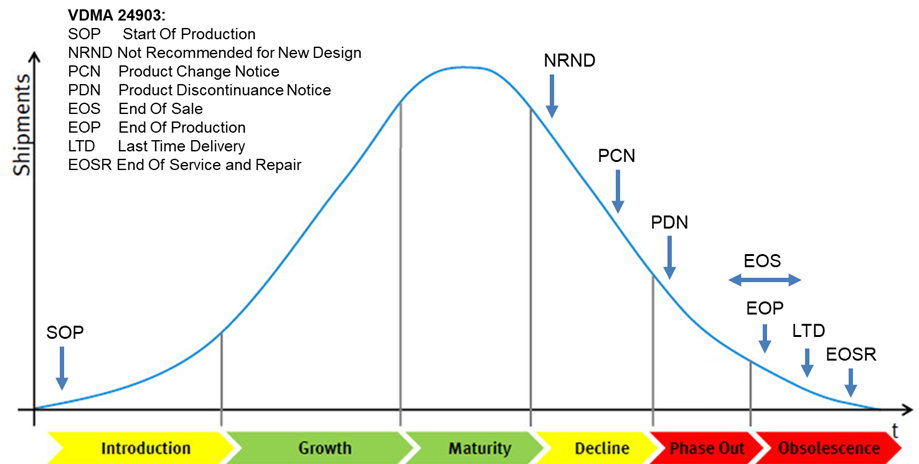
The VDMA 24903 standard for obsolescence management was created to define and compile all required terms as well as automate and standardize the exchange of information between companies regarding changes and discontinuations of products and units.
Reactive obsolescence management
Many companies treat cases of obsolescence purely reactively. Once a supply bottleneck has arisen, a somewhat murky process is set in motion to find a solution. As it happens so very often, a lack of time and limited options only allow for a rather costly selection of solutions.
To clearly regulate and coordinate this reactive process, to demurkify it if you will, every company should have an appointed obsolescence manager. Companies can have their employees trained as obsolescence managers at the HTV academy in cooperation with Amsys GmbH. HTV academy’s trainers are all certified by the IIOM (International Institute of Obsolescence Management).
Responsibilities of obsolescence managers
Obsolescence managers act in accordance with the standard
IEC 62402, which is kept up to date by members of the german industrial interest association COGD (Component Obsolescence Group Deutschland).
Obsolescence managers coordinate among other things how and where inside the company product change notifications and product discontinuation notices are documented. Many companies establish a specific internal email address for this purpose. Furthermore, obsolescence managers, in agreement with the managing directors, establish a basic obsolescence management guideline for the company, detailing exactly how obsolescence will be managed. They also draw up an obsolescence management plan (OMP) in cooperation with the affected departments in regards to individual products and devices, and they give the instruction lectures for the other employees.
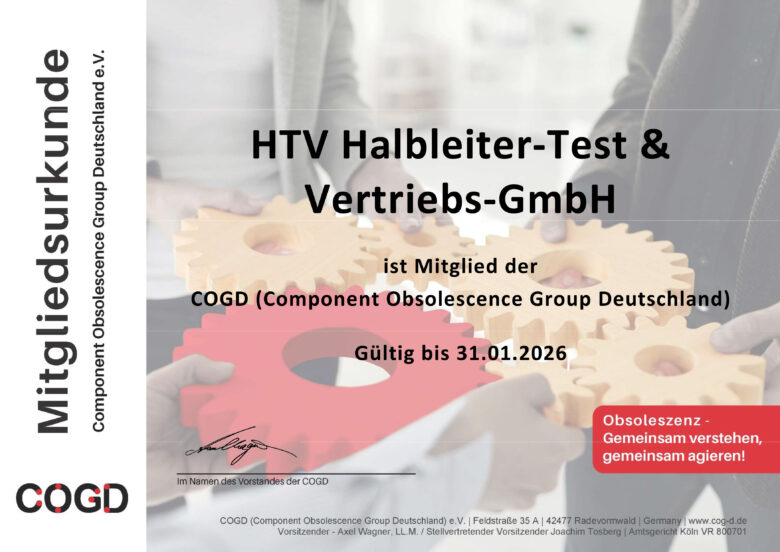
Obsolescence management guideline and obsolescence management plan (OMP)
An obsolescence management plan (OMP) for a product or a device contains all the necessary information to manage obsolescence both reactively and proactively, if required.
The obsolescence manager draws up the OMP in cooperation with the affected departments (such as purchasing, development, quality management, the managing directors, the customers, the manufacturers, the suppliers and and finances as well).
This plan details, among other things, the product or device with all its technological parameters and economical aspects (i.e., for how many years it should be produced) as well as how information should be exchanged with the customer. It is recommended to adhere to the VDMA (“Verband Deutscher Maschinen- und Anlagenbau” meaning the German Association of machine and fabrication plant manufacturers) standard 24903 for a uniform information exchange regarding PCNs and PDNs.
The portal pcngenerator.com is the perfect tool to document and transmit data in accordance with VDMA 24903 (such as manufacturer, customer part number (CPN), estimated production time, life cycle, estimated end of prodction (EOP) etc.).
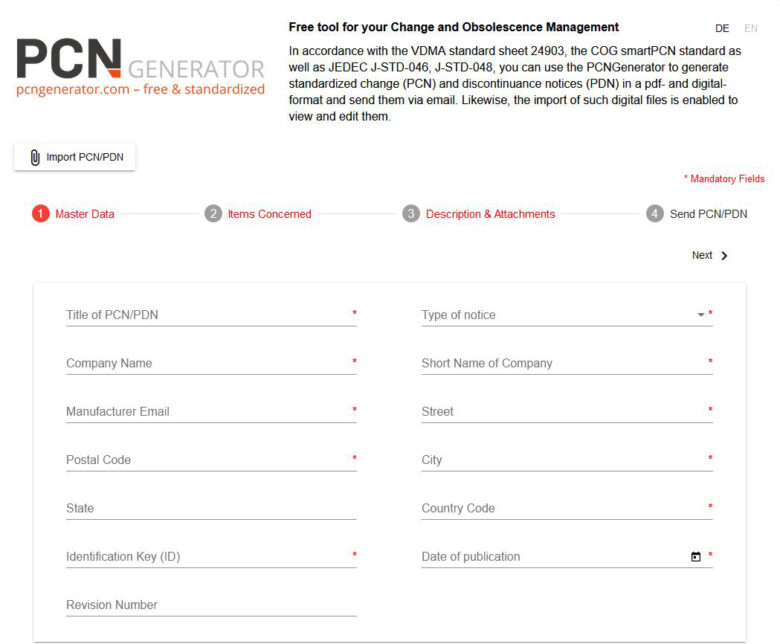
The OMP designates the smallest exchangeable units assembled in a product, which are usually listed in a product’s bill of materials (BOM). This data should also be routinely checked for its actuality by the obsolescence manager.
A decent data maintenance and accessabilit inside a company makes it possible to ascertain the effect a product change notification or a product discontinuation notice might have on other products.
Risk analysis for complex units
An obsolescence manager’s central task is designating whether a unit is to be classified as simple or complex in the OMP. Simple units are, among other things, standard design components, standardized components as well as proprietary products. These units are normally at a low obsolescence risk and can be dealt with reactively.
Complex units on the other hand are, among other things, purchased components, components with only very few alternative manufacturers and those components with very rare manufacturing technologies. Complex units require a risk analysis to ascertain the probability of obsolescence and its repercussions on affected products.
The most important parameters of a risk analysis are the number of a unit’s available manufacturers, an end of production forecast (EOP-forecast) and the current quantity on stock. The most important parameters of a risk analysis are the number of a unit’s available manufacturers, an end of production forecast (EOP-forecast) and the current quantity on stock. Amsys GmbH offers several fitting software products for an automated risk analysis.
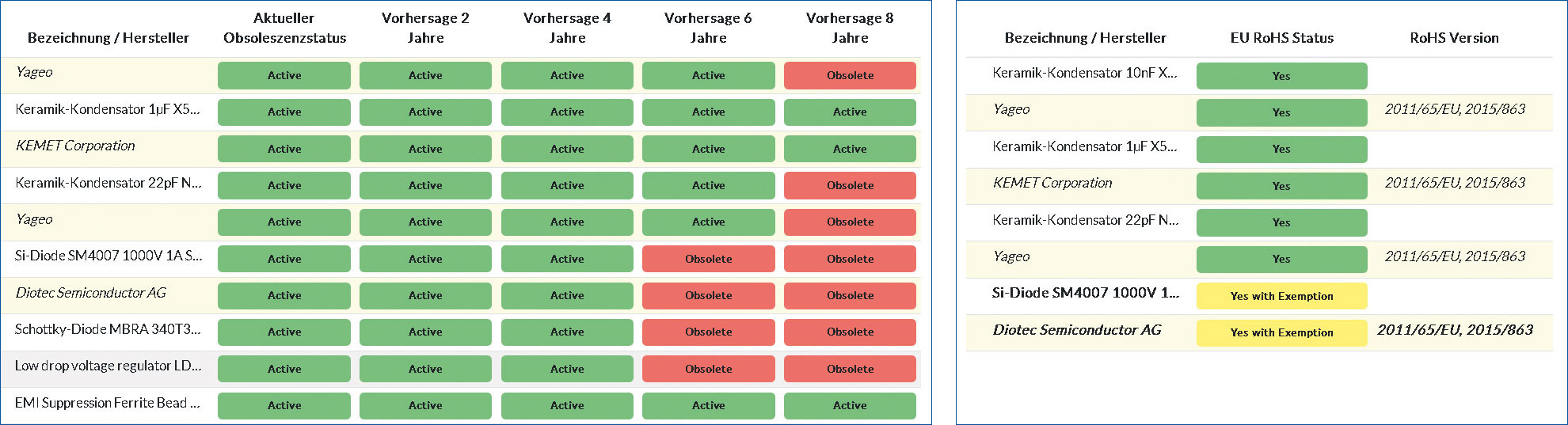
Corrective actions in cases of obsolescence
The OMP also includes a list of reactive and proactive solutions of which, if possible, always the the most cost efficient corrective measure should be chosen.
In comparison with a purely reactive obsolescence management, a proactive obsolescence management makes choosing the cost efficient solution possible by thoroughly monitoring the units. Reactive actions are, for example, the discontinuation of a proprietary product or the consumption of one’s own inventory.
It is usually necessary, should a unit be discontinued, to stock up in combination with long-term storage (storage time > 1 year).
In this case it is recommended to calculate the necessary remaining required amount of components and store those securely and without any aging effects using the HTV TAB® Long-Term Conservation for the needed amount of time.
Solution approaches and corrective actions in cases of obsolescence
„RA“ (Reactive approach) | „PA“ (Proactive approach) |
Discontinuing proprietary products | Planning a change in design |
Consuming available inventory | Stocking up proactively with Long-Term Conservation |
Reclaiming manufacturer agreements | Entering into agreements and partnerships with manufacturers |
Stocking up with Long-Term Conservation | Using sustainable technologies and materials |
Substituting an equivalent unit | Establishing transparency and modularity |
Substituting an alternative unit | Acquiring IPRs and/or software licenses |
Using aftermarket sources | |
Rework/Refurbishing | |
Repairing | |
Emulating | |
Redesigning small or big |
„RA“ (Reactive approach)
RA: Discontinuing proprietary products:
Should a company find themselves unable to manufacture products because of obsolescence they can discontinue the affected items themselves.
RA: Reclaiming manufacturer agreements:
If a discontinuation can be averted by designing an appropriate contract, this is a very simple and sometimes even very cost effective solution for dealing with obsolescence. Yet a redesign should be factored in proactively in case the manufacturer really does discontinue the production one day completely.
RA: Consuming available inventory:
If the inventory contains more units than which are necessary for the product’s planned life cycle the reach is sufficient. Discontinuing the affected unit does not threaten to interrupt production.
RA/PA: Stocking up (proactively) with Long-Term Conservation:
As long as components are still available on the market, they can be bought reactively in case of impending obsolescence or proactively during ongoing production. However, remnant components may be more expensive than the original components, but they make it possible to easily maintain production. Stocking up proactively aims to purchase the components early on to ensure that said components may be obtained in sufficient quantities.
RA: Substituting an equivalent unit:
If the necessary reach of a unit, such as an electronic component, can no longer be ensured by the available inventory, the obsolescence manager attempts, in cooperation with the development department, to find a component by an alternative manufacturer, which can substitute the original component in its form fit function interface specification (FFFIS).
RA: Substituting an alternative unit:
Sometimes howevery the obsolete unit may not be acquired exactly, but a cooperation between the OM and the development department may discover an alternative component, which can be substituted with slight modifications (such as adapting the software, adapting the production tools or using an adapter alltogether).
RA: Using aftermarket sources:
It is possible to obtain the components by other means than the original manufacturer.
RA: Rework/Refurbishing:
There is always the possibility that units from other products may be removed and inserted into the proprietary device (for example, electronic components may be desoldered from an unrequired assembly using the rework process).
RA: Repairing:
It is also possible that repairing an electronic assembly (such as during reworking) may lengthen its life cycle by replacing electronic components (units).
RA: Emulating:
Emulating the original unit with another unit is a very complex process. This may require investing a lot of time and money.
RA/PA: Redesigning small or big:
Redesigning can be, dependent on the scope, very cost-intensive, as it requires investing in development, possible certification as well as production. A redesigning process should therefore always be factored in proactively.
„PA“ (Proactive approach)
PA: Using sustainable technologies and materials:
Developers should actively receive guidelines to no longer include obsolete units in a product. This can be accomplished, among other things, by monitoring electronic components, technologies and materials.
PA: Establishing transparency and modularity:
Sensibly designing contracts and specifications can establish a modular approach to unit replacement. If a unit becomes obsolet it may no longer be necessary to exactly replace the affected unit, instead its functions and features may be implemented using an alternative unit. This approach may be impossible for certified products.
PA: Acquiring IPRs and/or software licenses:
If a unit is no longer in production, one solution may be to purchase or license the necessary expertise to produce the required unit maintain production through another manufacturer. This approach may be significantly less expensive than a redesign.