Critical material changes and aging processes of electronic components
Aging processes:
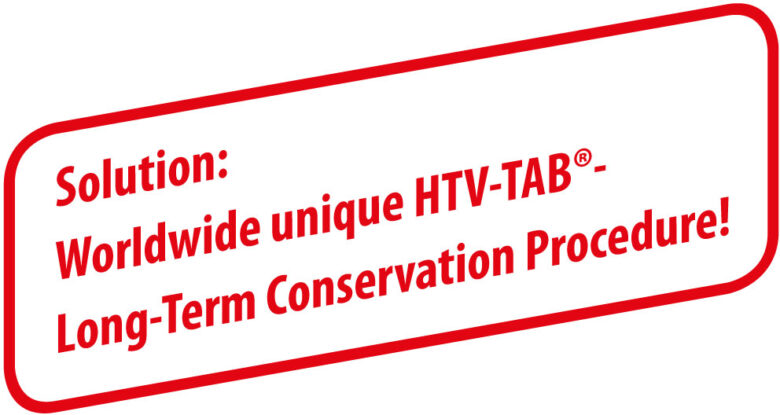
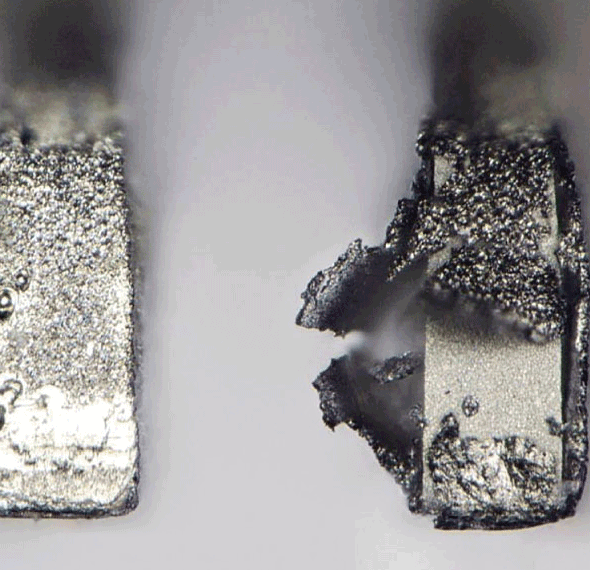
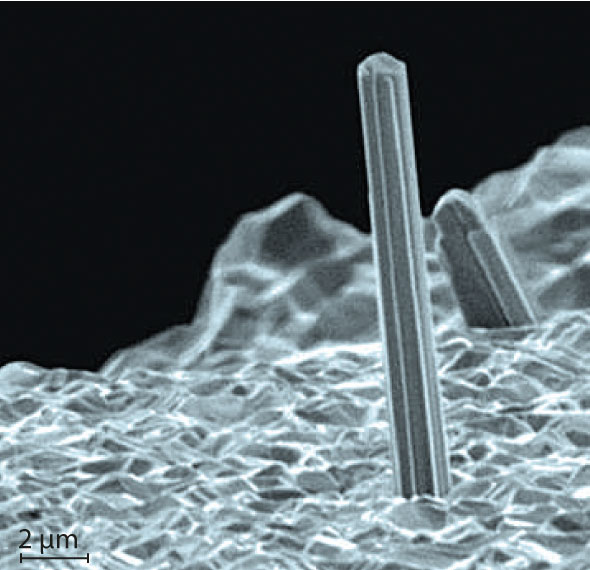
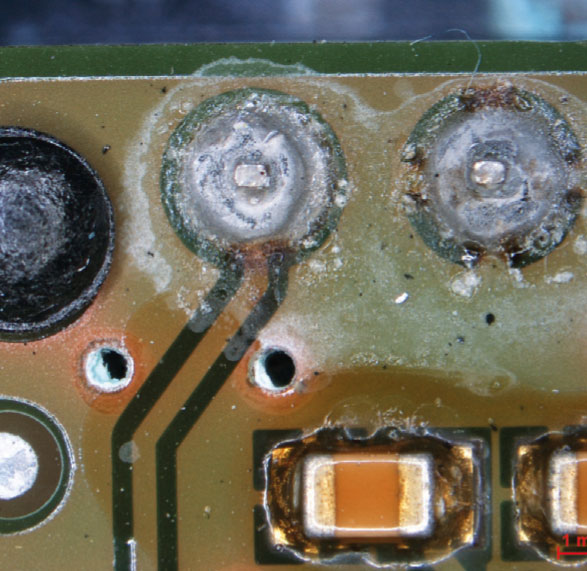
Already after two years, during normal storage condition as well as in nitrogen dry-pack, various aging processes impair the functionality (e.g. data and capacity losses, leakage currents) and processability (e. g. during the soldering process) of electronic components.
All aging processes need to be considered during Long-Term Storage and secured by suitable measures.
Diffusion processes
Diffusion is a physical process during which at least two or more substances are intermingling at an increasing rate. This is based on the thermally induced self-motion of particles like atoms, charge carriers or molecules. If the distribution of these particles is unevenly, more particles from the high concentration areas move to areas with a lower concentration than the other way around. Due to the thermal motion, differences in particle concentration are reduced until a complete intermingling (or equalization) has happened.
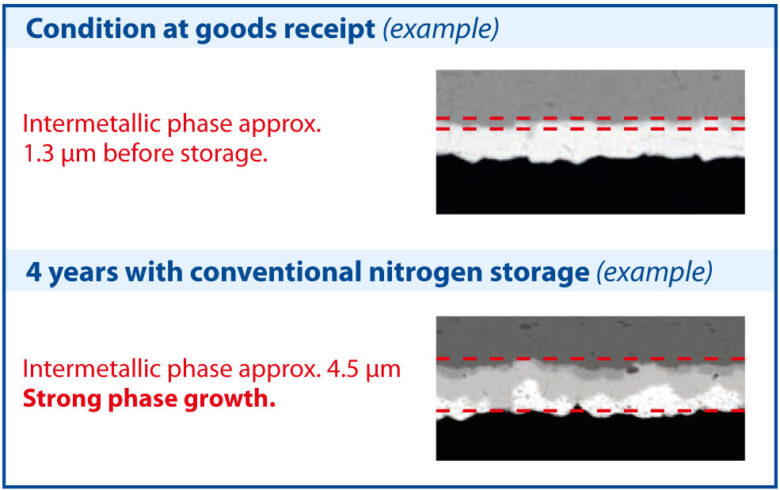
Diffusion processes, using intermetallic phase growth on pins as an example
Should, for example the copper or copper-iron substrate material of a contact pin diffuse into the tin, a completely new material similar to bronze is formed (intermetallic phase). Once this compound reaches the pin surface, soldering is no longer possible as intermetallic copper-tin alloys have melting points of over 400 °C, which can not be reached during typical soldering process temperatures of 240 °C to 280 °C. The tin is no longer capable of bonding with the pin carrier material of copper; thus, the solder contact can no longer be soldered.
Diffusion happens independent of any external energy supply, with the exception of temperature. The diffusion current (charge carrier current) also occurs in semiconductors at the pn-junction and depends on the temperature, the material, the type of charge carrier as well as on concentration differences in the doping of the semiconductors (n- and p-doped areas). In addition, the diffusion current generates an electric field, which causes a drift current flowing in the opposite direction of the diffusion current. The drift current increases over time until diffusion and drift current have reached a complete equilibrium (stationary state).
Diffusion is therefore a thermally activated process, in which the higher the temperature rises, the faster the transport of charge carriers becomes.
Diffusion also takes place inside the component, i.e., at chip level, and can have many different causes and effects.
Diffusion equations:
- Fick’s first law
- Fick’s second law
- Arrhenius equation
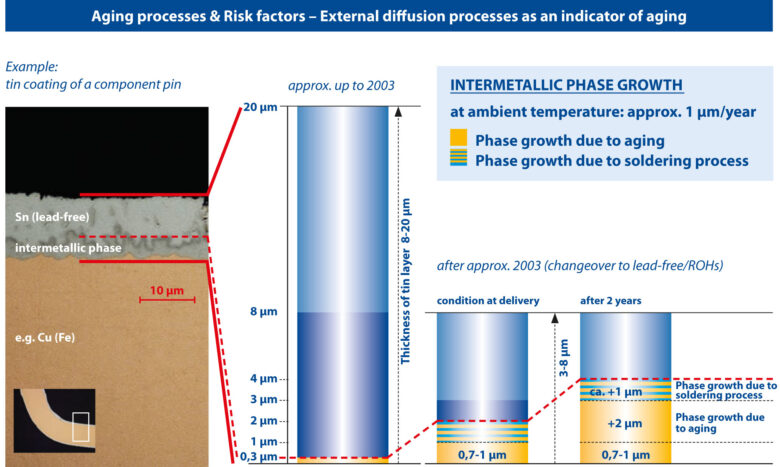
Aging due to moisture and oxygen (corrosion and oxidation)
Residual oxygen and possible moisture in conventional nitrogen dry-packs causes oxidation and corrosion processes at component connections and contact surfaces as well as at bond pads on bare-DIEs and wafers. Getting reliable soldering or bonding connections becomes difficult after a while, or outright impossible in some cases.
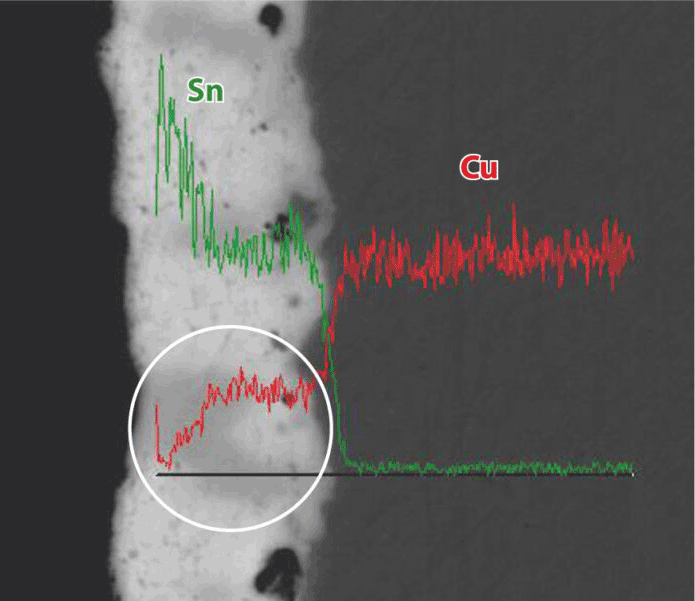
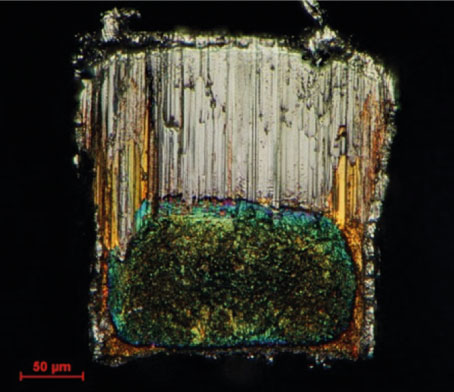
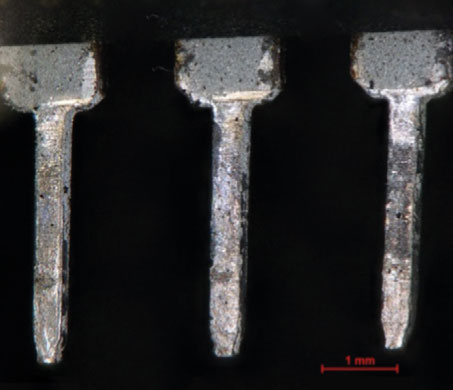
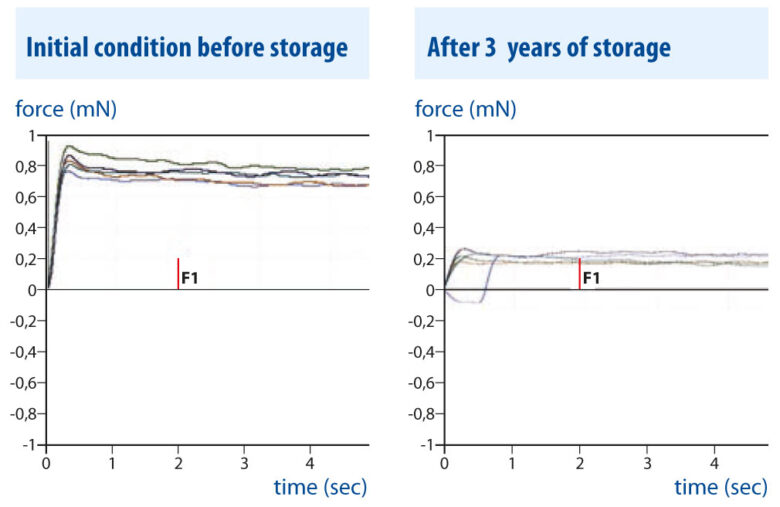
Aging due to hazardous substances
Outgassing of additives such as plasticizers, flame retardants, solvents or stemming from repackaging can cause corrosion of component connections and contact surfaces and thus negatively affect the solderability of the electronic components. An analysis using GC-MS of the special HTV absorption material after different storage times shows that a high content of hazardous substances such as styrene, toluene, ethylbenzene, xylenes and aromatic hydrocarbons is already present after 3 years in a standard dry pack with BGA components.
Connector sockets – looking good on the outside, but what is hiding under their metal cover?
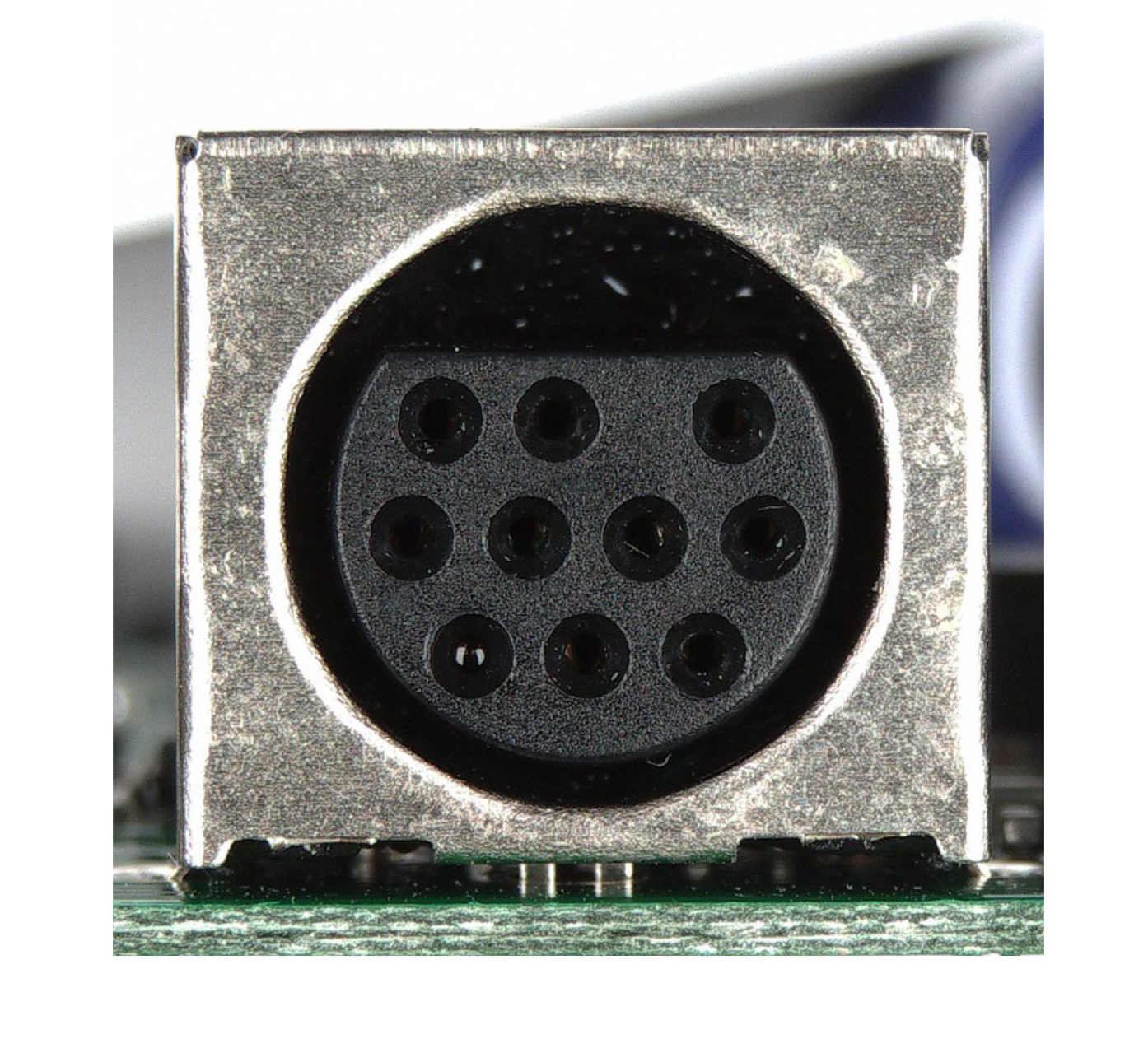
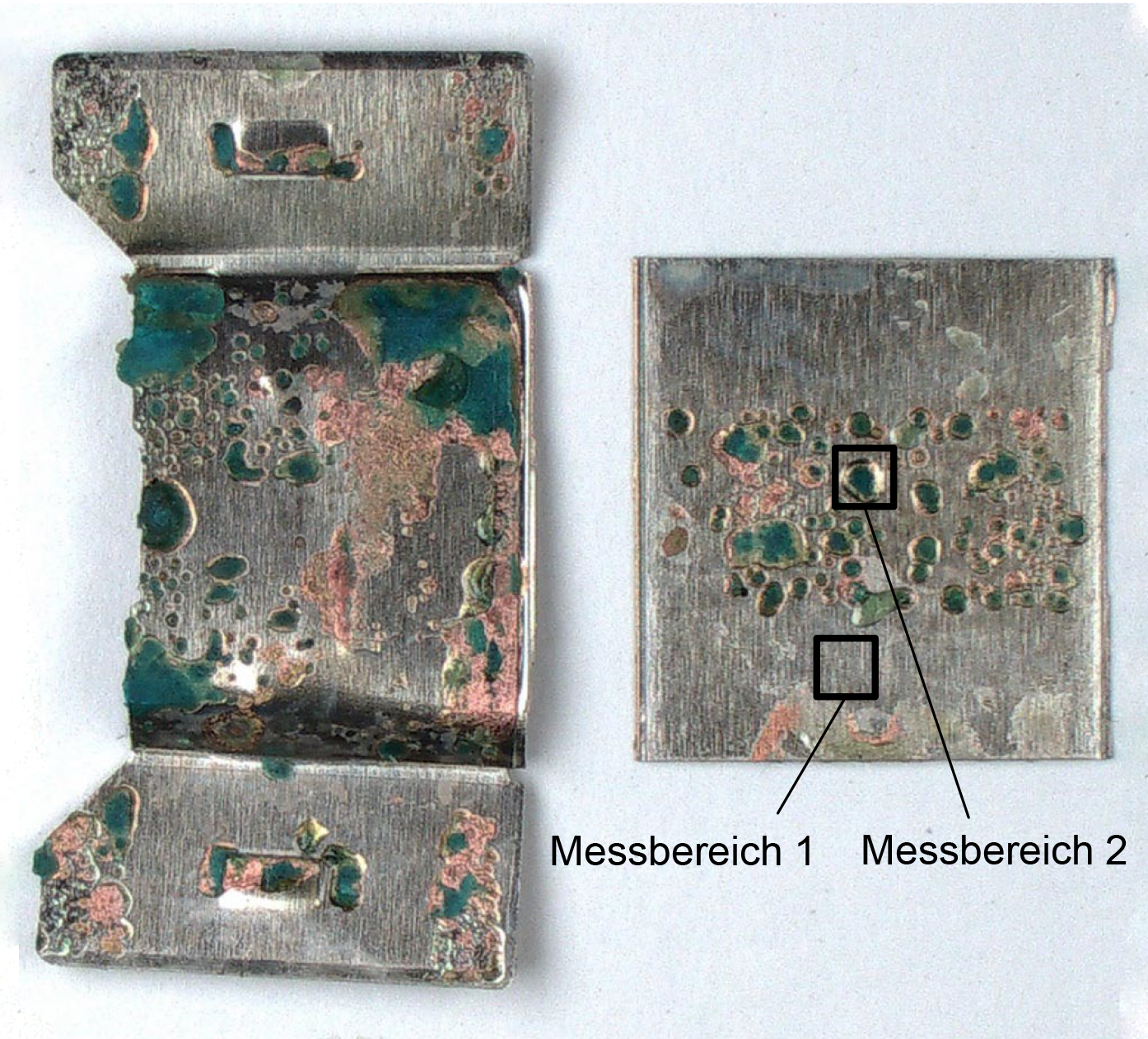
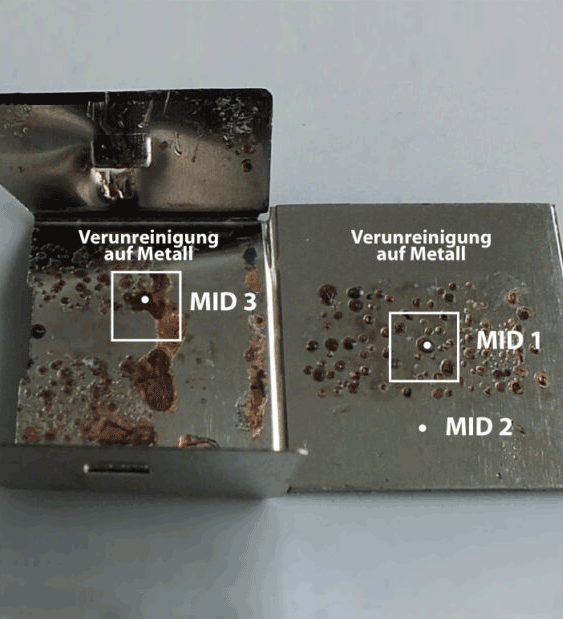
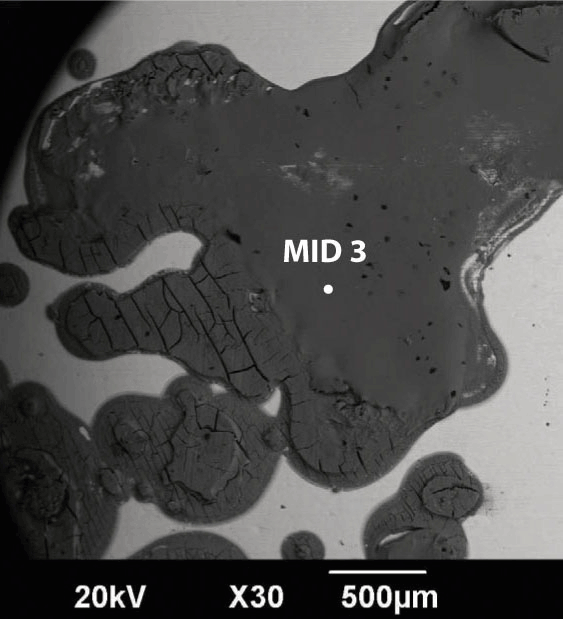
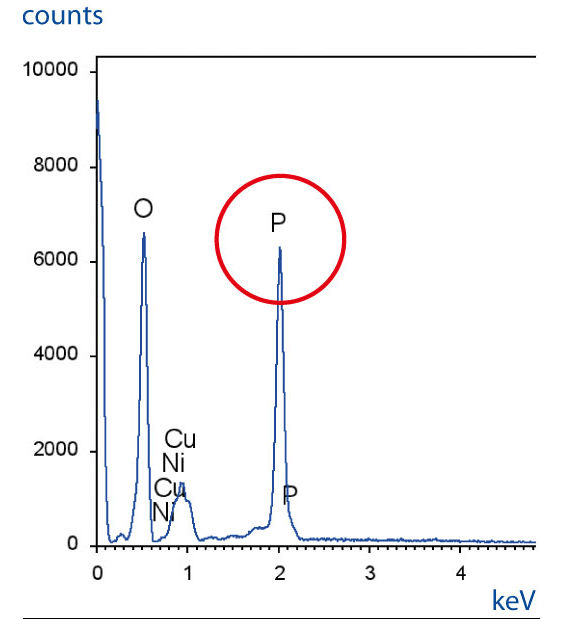
EDX spectrum
These problems can can be avoided by the HTV-TAB® method which uses specifically adjusted hazardous substance absorbing materials to bind potential outgassings. This prevents material level interactions between hazardous substances and the components’ materials, as can be seen in the examples above.
Analyses of affected hazardous substance absorbing materals via GC-MS (gaseous chromatography and mass spectrometry), following different timespans of storage, prove. that there is a high concentration of hazardous substances such as styreme, toluene, ethylbenzene, or xylene as well as other aromatic and aliphatic hydrocarbons, after merely 3 years in a standard drypack containing BGA components.
Whiskers
The formation of whiskers (finest single-crystal tin needles), often resulting from mechanical stress within electroplated tin layers on the lead frame or within corrosion and oxidation layers on the tin surface or from intermetallic phase growth, can and will significantly impair the functionality of electronic components, as they can cause short circuits between component connections and probably malfunctions and component damages.
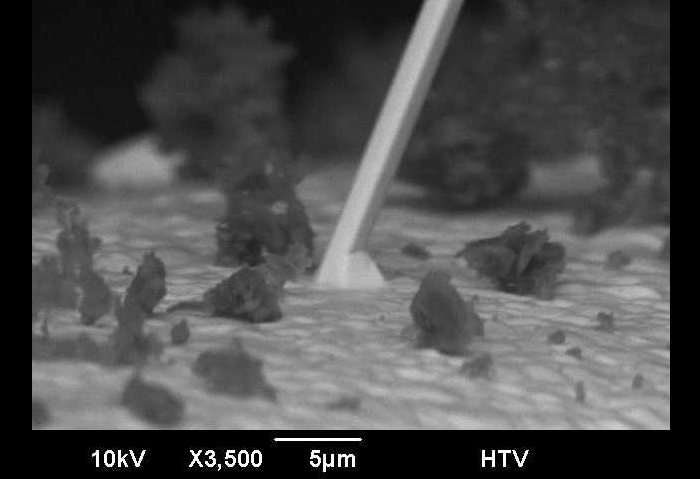
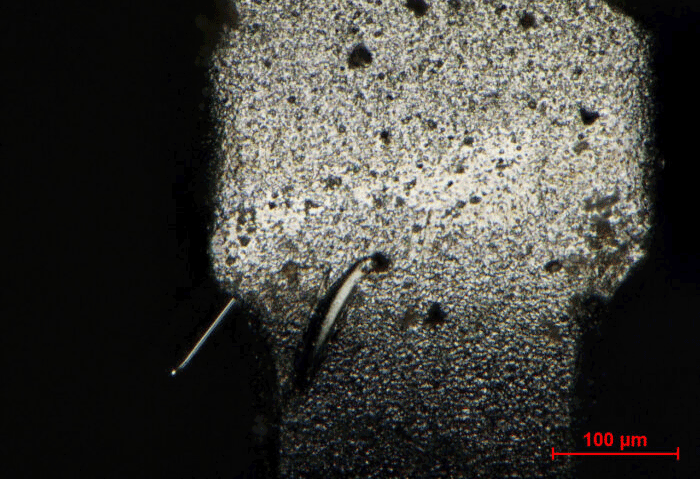
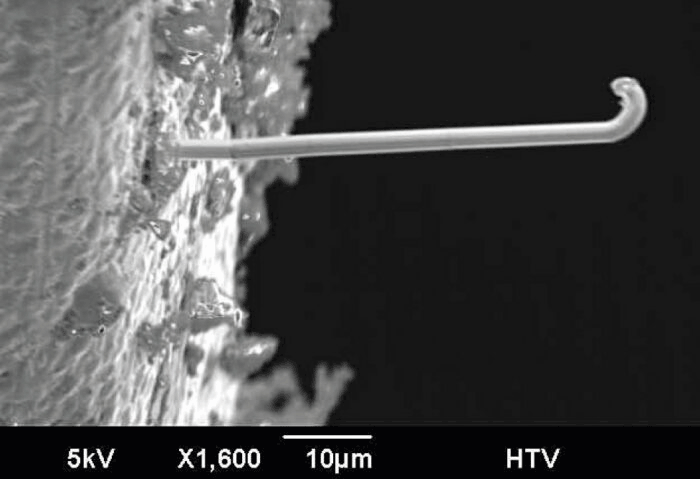
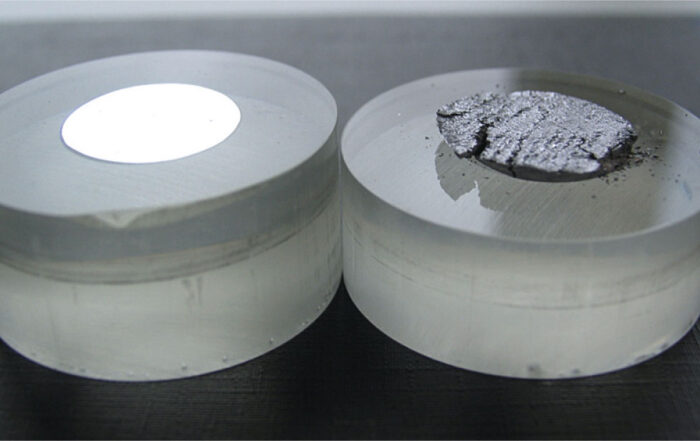
Tin pest
At temperatures below 13.2 °C silver-white, metallic β-tin can convert into the grey-black α-tin, which has a different crystalline structure and density. Since α-tin has a larger volume than β-tin, the material loses its integrity, the grain structure dissolves and tin powder is formed, which can no longer be soldered.
Aging processes in assemblies
Due to the enormous variety of types and combinatorics of the individual components, assemblies often show additional aging effects which can endanger the proper functionality of the entire assembly. Especially during long-term storage, outgassing from used coatings and potting compounds as well as residues from the soldering process can lead to corrosion and oxidation of the assembled components. In addition, capacitors (especially electrolytic capacitors) run the risk of changing their capacity or increase the leakage current during storage, which can result in total failure and thus destruction of the entire assembly. LC or OLED displays are at risk of a significant change in their optical properties as well.